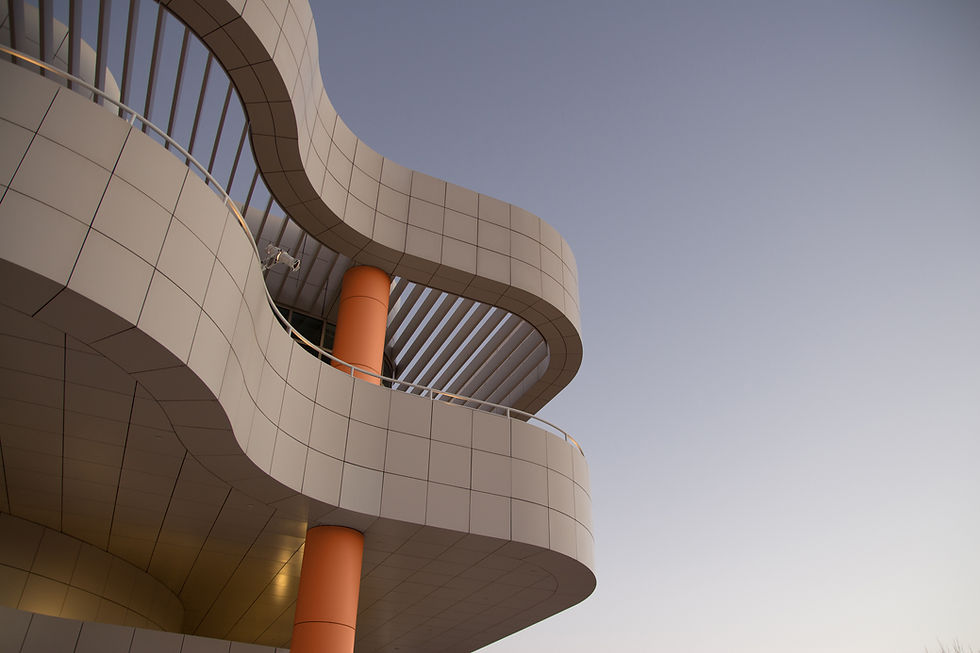
Electric Vehicles: Debunking the Myths and Addressing the Real Fire Risks
Aug 20, 2024
6 min read
0
43
0
Electric vehicles are known to be a more environmentally friendly alternative to the traditional gas- and gasoline-powered cars. However, concerns about electric vehicle (EV) fires have increased amidst the growing adoption of EVs, leading to global safety concerns. In addition, electric vehicles are being banned from parking in underground parking lots due to fears of battery explosions that occurred in South Korea. For example, in Incheon, a Mercedes-Benz EQE caught fire in an underground parking lot, damaging vehicles and restricting EVs in such spaces. This article emphasized the challenges of managing EV fires, especially due to the intense heat and potential for significant damage in such environments. Therefore, despite their environmental benefits, the inherent safety risks of EVs pose significant challenges that must be addressed to ensure widespread adoption without compromising public safety.
(Image by iStock)
People have become more cautious about electric vehicles because, unlike traditional car accidents, they believe there are many unpredictable factors involved. Moreover, finding the solution to EV spontaneous fires presents unique challenges that differ from traditional vehicle fires. EV fires typically involve lithium-ion batteries, which can undergo thermal runaway. The thermal runaway process in lithium-ion batteries, particularly those using NCM/Graphite electrodes and a PE-based ceramic-coated separator, involves a self-reinforcing Heat-Temperature-Reaction (HTR) loop. Initially, heat triggers sequential reactions such as the decomposition of the Solid Electrolyte Interphase (SEI) and the melting of the separator, leading to further temperature increases. As this cycle continues, the ceramic coating on the separator eventually fails, resulting in a massive short circuit that culminates in a thermal runaway. These reactions are difficult to predict and can spread quickly once they begin. In addition, unlike traditional vehicle fires, EV fire is more likely to reignite after the fire is believed to be extinguished as chemical reactions within the battery can continue, potentially leading to an intense fire again that is difficult to extinguish. Moreover, putting out a lithium-ion battery fire requires upwards of 3,000 gallons of water, which is far more than what is needed for a typical fire. Therefore, this phenomenon is particularly concerning in high-energy-density batteries, underscoring the need for robust design and monitoring systems.
(Image by iStock)
Moreover, in electric vehicles, a Battery Management System (BMS) plays a crucial role by monitoring parameters such as temperature, voltage, and current and ensuring that the battery operates within safe limits. However, if the BMS malfunctions or has defects, it may fail to detect overcharging, over-discharging, or overheating, leading to dangerous situations like thermal runaway. Therefore, implementing a reliable BMS is crucial to preventing battery fires. To establish a dependable BMS, developing AI that can predict potential risks by detecting the battery’s performance and state, and integrating it into the BMS, can provide early warnings and further enhance safety.
Electric vehicles offer environmental benefits, but they also pose unpredictable dangers that differ from traditional gas-powered cars. Therefore, it is essential to take measures like developing a Battery Management System.
(Image by iStock)
Electric vehicle fires can be caused by overcharging or over-discharging the battery pack. The battery packs are composed of cells connected in series or parallel to meet the power demand. During discharging, the cell with the lowest state of charge (SoC) will reach the minimum safe operating voltage first, requiring the BMS to shut off operation. Similarly, during charging, the cell with the highest SoC will reach the maximum safe operating voltage first, prompting the BMS to halt the charging process. If this process repeats, it reduces efficiency and leads to overheating, which is the primary cause of the fires. In the battery pack, the cells can not be the same while they have equal SoC but should be balanced to prevent overcharging and over-discharging. So, maintaining cell balancing is a crucial function in the Battery Management System. There are two ways, including passive cell balancing and active cell balancing. Passive cell balancing involves achieving voltage equalization about the SoC by dissipating energy through a resistor. To achieve balance, the difference between the cells with the highest SoC levels and the SoC levels of other cells must be evaluated. Afterward, it takes in the surplus energy and releases it through the resistors, thereby leveling the SoC for all the battery cells. But there is the wastage of energy as heat when equalizing the cells via resistors. The heat affecting the cells can cause overheating, the main reason for thermal runaway. So, currently, passive cell balancing is not used because of the drawback. In active cell balancing, voltage samples from all cells are gathered, and the average is computed. Then, it redistributes the charge from cells exceeding the average to those below the average. In contrast to passive cell balancing, active balancing delivers strong performance even in the presence of batteries with different capacities. It saves and preserves surplus energy, thereby enhancing battery efficiency. Therefore, recently, active cell balancing has been used for electric vehicles. However, active balancing also has a disadvantage, which is a loss of energy (10-20%) while transferring energy among cells. Even though active cell balancing has better efficiency than passive cell balancing, there is indeed a loss of energy when energy is transferred. The loss of energy is formed as heat, which mitigates the efficiency of the battery cells leading to overheating. Hence, preventing not to lose the energy is important when the researchers make the structure of battery cell. Active cell balancing necessitates an extra circuit within the battery pack to facilitate the balancing process between cells. It uses any one of the energy transformation techniques to transfer energy between cells, called equalizers. The BBC (Buck-Boost convert) is also one of the transformation measurements. There are equalizers, including capacitors, inductors, transformers, and DC/DC converters. CBCB (Capacitor-based Cell Balancing) requires a single capacitor used to store and transfer the charge from the higher-capacity cell to the lower-capacity. The topology aims to minimize the need to bypass battery cells in order to improve cell balancing speed. The Inductor-Based Cell Balancing only requires a single inductor to transfer charge from a higher potential cell to a lower one. In the technique known as Transformer-Based Balancing (TBB), a specialized transformer is employed in a setup with a primary and single-secondary configuration to redistribute energy among cells. The equalizer is based on a DC/DC converter. DC/DC converter transfers the energy to match the voltage levels. According to research that Ontario Tech University conducts, The CBCB raises an issue due to the aging of the battery cells, leading to decreased effectiveness in voltage balancing because of cell-cap variations. The TBB approach is considered uneconomical as well.
(Image by iStock)
Moreover, the DC/DC converter features a more intricate circuit, resulting in a more resilient system capable of addressing various issues. With Capacitors and inductors, it can be used to minimize inrush current and lower the likelihood of overvoltages, causing low-efficiency loss, higher accuracy, allowance for voltage differences, bi-directionality, and low ripple. I wanted to find more specific information on the use of DC/DC converters due to the advantages they offer based on research. So, I found that there are Non-isolated DC/DC Converters and Isolated DC/DC Converters. The connection between the input and output circuits is the distinguishing factor among these converters. And I thought that this connection also affects the efficiency of active cell balancing. So, I suggest using a non-isolated converter to enhance active cell balancing, thereby preventing overcharging and over-discharging. The reason I recommend using a non-isolated converter is that the input and output may influence each other since they are interconnected within a single circuit, raising the efficiency of the active cell balancing. Moreover, the article conducted by INTEGRA SOURCES highlights that non-isolated DC/DC converters have benefited from their relatively low cost, smaller size, and higher efficiency compared to isolated models.
(Image by iStock)
In addition, research published in IEEE proposed a new topology based on a non-isolated DC/DC converter and a low-speed switching matrix to overcome the efficiency and power limitations of present balancing methods. This research shows that the newly proposed method improved overall balancing efficiency by up to 47.4% and reduced balancing time by up to 36.9% when they studied cases with eight randomly distributed battery cells. Another research that VIT University conducts proposes the architecture uses a non-inverting buck-boost converter (NIBBC) that is one of the non-isolated converters. This study utilized a combination of buck-boost and switched capacitor configurations to enhance the balancing speed and efficiency of batteries. This study proved that the results show a balancing speed of 1328s and a balancing efficiency of 97.05%. Therefore, according to the researchers who made topologies by using non-isolated converters, utilizing the non-isolated converters to transfer the charge for active cell balancing can be the way to improve the efficiency and prevent over-charging and over-discharging that leads to thermal runaway.